SANMOTION Model No.PB ( Closed Loop )
Closed loop stepping systems combine the advantages of two types of motors; they are easier to use than servo systems, and more reliable than stepping systems. Their unique control method eliminates the step-out of stepping motors. Also, they have no vibration when stopped, and short stroke positioning time is shortened considerably. Simple to operate, they contribute significantly to system construction cost saving.
Lineup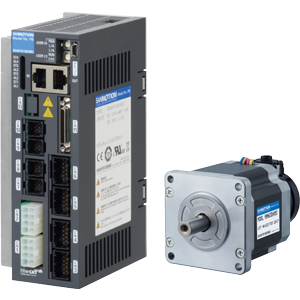
No step-out and zero micro-vibration when stopped
The position detection sensor automatically switches to closed loop control (servo motor control type) when rotating, and open loop control (stepping motor control type) when stopped. This eliminates both the step-out phenomenon that affects stepping motors, and the hunting phenomenon that affects servo motors, and contributes to reduced vibration and increased equipment reliability.
Positioning time is shortened by high torque in the low speed rotation area
With high torque at low rotation speeds, positioning time is decreased in the short stroke and high hit rate area. And, as it has higher torque characteristics at low speeds than conventional servo motors, system size can be reduced.
Optimized electric current supply reduces motor heating and decreases vibrations
By optimally controlling current to match loads, and supplying the minimum electric current to generate the required torque, motor temperature was significantly reduced compared to stepping systems that receive the maximum current at all times.
The rotor position is monitored and controlled so the optimum excitation timing is always achieved. By controlling the excess current, vibration can be decreased. Reduced motor heat and vibration enables high frequency operation, and contributes to higher efficiency and lower equipment power consumption.
Easy operation and safe protective functions
The encoder continually confirms rotor position. In the event of abnormalities such as voltage, load, or temperature, various alarms can be issued, providing the reliability of servo motors. Also, user-friendly features are available, such as setting and monitoring positioning and speed information through PC interface software.
High-speed EtherCAT field bus interface
EtherCAT is a 100 Mbps high-speed and high reliability fieldbus system.
System control can be improved with high response performance, dramatically shortening cycle time.